Schweißfehler: Ursachen und typische Fehler
Aufgrund des Zusammenwirkens vieler physikalischer Größen kann es während des Schweißens zu einer Reihe von Schweißfehlern kommen. In diesem Beitrag möchten wir ein paar Hintergrundinformationen über häufige Fehler beim Schweißen vorstellen.
Diese Fehler können das Resultat einer falschen Schweißtechnik oder Maschineneinstellung sowie eines nicht berechneten Einflusses von außen sein. Beispiele hierfür sind ein falsch eingestellter Schweißstrom oder Zugluft. Form und Größe der Schweißnaht spielen nur eine untergeordnete Rolle, weil fast alle Fehler bei jeder Schweißnaht auftreten können.
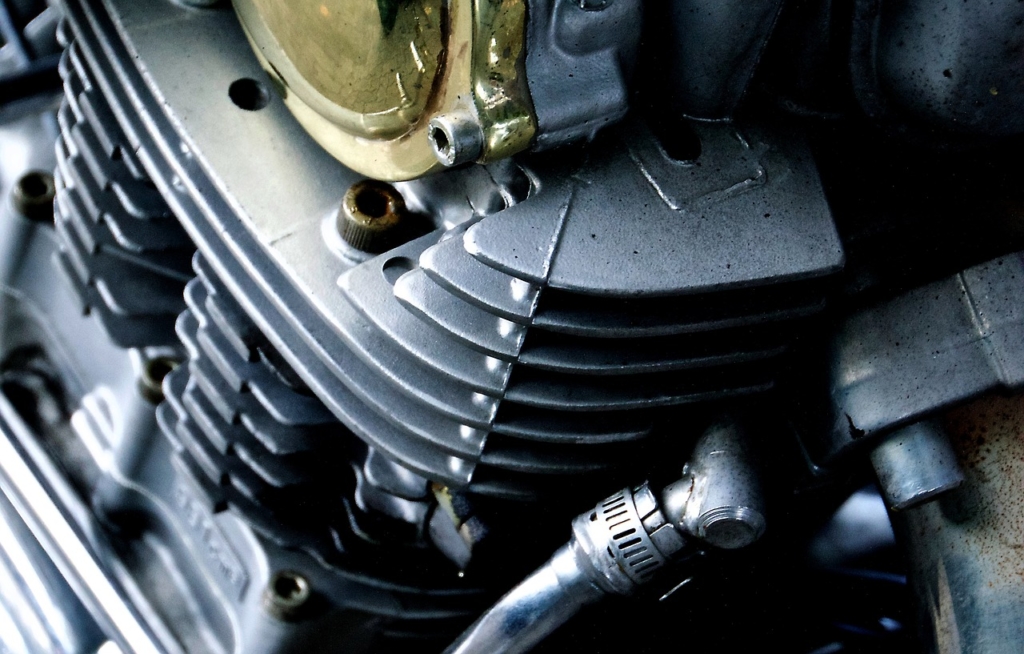
Welche Arten von Schweißfehlern können auftreten?
Dieser Abschnitt handelt von den häufigsten Fehlern sowie deren Ursachen und den Möglichkeiten ihrer Vermeidung.
Hohle Einschlüsse
Hohle Einschlüsse können grundsätzlich bei jeder Schweißnahtform und Größe auftreten. Zu einem Einschluss kommt es meist dadurch, dass sich beim Schweißen entstehende Gase in der Schmelze sammeln und diese Stellen blockieren, wodurch ein Hohlraum entsteht. Diese Einschlüsse können entweder punktuell oder auf der gesamten Länge der Schweißnaht vorkommen. Ist der Hohlraum rund, bezeichnet man ihn als Pore. Entsteht er durch die Schrumpfung des Materials beim Abkühlen, wird er Lunker genannt.
Die Ursache dieser Hohlräume kann unter anderem in einer hohen Feuchtigkeit, falschen Schweißparametern oder einer übermäßigen Verwendung von Hilfsstoffen wie Schutzgas bedingt sein.
Feste Einschlüsse
Feste Einschlüsse entstehen durch das Eindringen von Fremdkörpern in die Schweißnaht. Diese Fremdkörper schwächen die Schweißstelle nachhaltig und können aus der erkalteten Schweißnaht nicht ohne Aufwand entfernt werden. Bei diesen Fremdkörpern kann es sich beispielsweise um Schlacke oder Oxidbeläge handeln.
Sollten diese Einschlüsse vermehrt auftreten, liegt das häufig an falschen Einstellungen des Schweißgerätes, wenn etwa zu wenig Schutzgas verwendet wird. Einflüsse anderer Arbeitsplätze, etwa durch umher fliegende Späne von Schleifarbeiten, sollten ebenfalls ausgeschlossen werden.
Riss
Ein Riss entsteht in der Regel durch mechanische Spannungen. Das Werkstück besitzt aufgrund seiner Struktur eine Eigenspannung, welche sich beim Erhitzen und Abkühlen stark verändert. Der Riss tritt somit höchstwahrscheinlich beim Ausdehnen oder Zusammenziehen des Materials sowie an den Zündstellen von elektrischen Schweißgeräten auf. Ein Riss kann dabei viele Formen haben und macht schlimmstenfalls die gesamte Schweißnaht unbrauchbar. Man unterscheidet verschiedene Arten von Rissen, unter anderem den Endkraterriss, Hutriss, Längsriss oder Querriss.
Die während der Schweißung entstehende Temperatur kann in gewissen Grenzen über Spannung und Strom des Schweißgerätes reguliert werden. Es könnte allerdings auch das Einwirken von ungünstigen Umgebungsbedingungen, wie beispielsweise einer niedrigen Außentemperatur oder kalter Zugluft, für Risse von Material und Schweißnaht verantwortlich sein.
Schweißverzug
Der Schweißverzug entsteht, genau wie der Riss, durch die Wechselwirkung von Ausdehnung und Schrumpfung. Je nach Art und Größe der Schweißnaht können verschiedene Formen des Schweißverzuges auftreten. Beispiele sind die Längsschrumpfung, Querschrumpfung oder der Winkelverzug. In extremen Fällen ist der Schweißverzug so stark, dass sich das Endmaß des Werkstückes für das bloße Auge sichtbar verändert.
Diesem Fehler vorzubeugen ist sehr schwierig, da eine gewisse Hitzeentwicklung beim Schweißen unvermeidbar ist. Die Temperaturentwicklung kann allerdings beeinflusst werden, indem beispielsweise die Schweißnaht nicht in einem Zug gezogen wird, sondern in mehreren Stücken mit kurzen Pausen. Bei langen Nähten kann man außerdem zwischen Anfang und Ende der Naht hin- und herwechseln.
Ungenügende Durchschweißung
Eine ungenügende Durchschweißung bedeutet, dass die Werkstücke nicht auf ihrer kompletten Dicke miteinander verschweißt wurden. Dies hat eine stark verminderte und einseitige Belastbarkeit zur Folge. Die Ursache des Fehlers kann eine zu schnell gezogene Schweißnaht oder eine zu geringe Wärmezufuhr sein.
Zündstellen
Die sogenannten Zündstellen entstehen dadurch, dass der Schweißlichtbogen durch Berühren des Materials entzündet werden muss. An dieser Stelle entsteht durch ungünstige Temperaturverhältnisse eine punktuell unsaubere Schweißnaht mit einer geringeren Festigkeit und einer erhöhten Bruchgefahr.
Zur Vermeidung des Fehlers wird der Lichtbogen entweder über der bereits fertigen Naht gezündet oder an einer Stelle, welche im Verlauf noch komplett überschweißt wird. Auch ein nachträgliches Erhitzen der Schweißnaht an Zündstellen ist möglich.
Wasserstoffversprödung
Ein besonders tückischer Fehler ist die Wasserstoffversprödung. Hierbei handelt es sich um einen Einschluss von Wasserstoff im Inneren des Metalls. Dies führt zu einer Korrosion, welche von innen beginnt. Das gefährliche an diesem Schweißfehler ist, dass er nicht unmittelbar nach der Schweißung auftritt. Wie bei jeder Form von Rost und Korrosion kann es Tage oder Wochen dauern, bis der Fehler auf der Oberfläche sichtbar wird.
Um der Wasserstoffversprödung vorzubeugen werden in der Metalltechnik verschiedene Wärmeverfahren eingesetzt, die eventuell eingeschlossenen Wasserstoff aus dem Metall ausleiten sollen.
Welche Folgen hat ein Schweißfehler?
Alle Arten der Schweißfehler eint die Schwächung der Schweißnaht an der Fehlerstelle.
- Ein Lufteinschluss beispielsweise sorgt für eine punktuell verminderte Belastbarkeit und erhöht die Bruchgefahr in diesem Bereich. Tritt dieser Einschluss an einer kurzen Schweißnaht auf, kann er deren gesamte Funktion gefährden.
- Risse bringen die große Gefahr mit sich, dass die Schweißnaht und das Werkstück immer weiter reißen. Die gerissene Stelle sorgt nicht nur für eine niedrigere Belastungsgrenze, sondern hat zur Folge, dass die Bereiche neben dem Riss verstärkt belastet werden. Es besteht also eine akute Gefahr, dass sich der Riss ausbreitet.
- Erneuter Bruch: Ein ähnlicher Effekt kann oft beobachtet werden, wenn ein gebrochenes und geschweißtes Teil neben der Schweißnaht erneut bricht. Hier wurde die Bruchstelle durch Verstärkung der ursprünglichen Bruchstelle lediglich verlagert.
- Die Wasserstoffversprödung beginnt mit einer Korrosion von innen heraus, indem sich Wasserstoffatome im Metallgitter ablagern. Dies führt zu einer, wie der Name verrät, Versprödung des Materials, also einer Verringerung der Belastbarkeit. Dadurch kommt es bei einer Wasserstoffversprödung auf lange Sicht häufig zu sehr großen Rissen.
Besonders bei Bauteilen, deren Fehlfunktion Menschenleben gefährden könnte, sollten deshalb Gegenmaßnahmen ergriffen werden.
Wie werden Schweißfehler ausgeschlossen?
Da nicht alle Schweißfehler mit dem Auge von außen erkennbar sind, müssen für Schweißnähte mit besonderen Anforderungen auch spezielle Prüfverfahren eingesetzt werden. Man benutzt hier meist sogenannte zerstörungsfreie Prüfverfahren, bei denen das Werkstück nicht beschädigt wird. Beispiele für derartige Prüfungen sind das Röntgen oder die Ultraschalluntersuchung. Diese Prüfungen haben den großen Vorteil, dass sie nicht nur Fehler auf der Oberfläche erkennen, sondern die gesamte Schweißnaht durchleuchten.
Das Gegenstück zu den zerstörungsfreien Prüfungen bilden die zerstörenden Prüfungen. Es gibt diverse Varianten der zerstörenden Werkstoffprüfung, welche dazu gedacht ist, die Belastungsgrenze des Werkstücks herauszufinden. Beispiele sind der Torsions-, Biege- oder Scherversuch.
Der große Vorteil zerstörender Werkstoffprüfungen ist, dass die tatsächliche Belastungsgrenze des Werkstücks ermittelt wird. Der Nachteil ist, dass das Werkstück dabei zerstört wird und daher nur stichprobenartig geprüft werden kann. Kurzzeitig auftretende Störungen im Schweißprozess werden somit eventuell nicht entdeckt.
FAQ
Einige Schweißfehler tauchen häufiger auf als andere, hier finden Sie eine Übersicht mit häufigen Fehlern:
– Hohle Einschlüsse
– Feste Einschlüsse
– Riss
– Schweißverzug
– Ungenügende Durchschweißung
– Zündstellen
– Wasserstoffversprödung
Einfach klicken für weitere Informationen.
Natürlich steht an erster Stelle das Können. Daher sollte man das richtige Schweißgerät, die richtige Technik einsetzen, das lernt man aber zu Beginn.
Aber auch Profis kann mal ein Fehler unterlaufen, daher gibt es Prüfmethoden.
– Zum Beispiel Röntgen oder die Ultraschalluntersuchung.
– weiterhin gibt es zerstörende Werkstoffprüfungen, hierbei werden die Belastungsgrenzen der Werkstücke ermittelt.